Cold Heading Rivet Nut, a cold - formed fastener, is used in aerospace, automotive, construction machinery, energy equipment, etc., providing reliable equipment assembly and connection solutions.
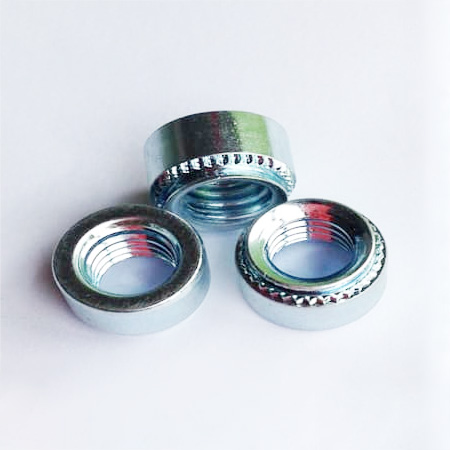
Production Process
The production involves several steps. First, raw materials are annealed for proper hardness. Then, cold heading forms the blank, followed by degreasing, local annealing, pickling, etc. Next, machining creates internal threads. Finally, surface treatment and testing ensure mechanical properties and quality.
Material Selection
Material selection is crucial. Common materials are aluminum, steel, and stainless steel. Aluminum rivet nuts are for aluminum component connections, while steel and stainless steel ones have broader applications. Considerations include corrosion resistance, strength, and compatibility with connected materials.
Installation Method
Installation requires professional tools. Place the rivet nut accurately, then use a riveting tool to apply pressure, making the head or flange tightly adhere to the connected part for a secure connection. Proper installation is vital for connection strength and reliability.
Quality Standards and Inspection
Cold Heading Rivet Nuts must meet relevant standards. During production, strict inspection of dimensions, thread accuracy, and mechanical properties occurs. For example, strength must reach 8, 10, or 12 grades to ensure reliability and safety. Advantages
Compared to traditional welded nuts, Cold Heading Rivet Nuts avoid welding - related defects and risks. Their installation is simple and quick, improving efficiency. The cold - heading process gives them high strength and good mechanical properties for harsh conditions. Market and Suppliers
Many suppliers offer Cold Heading Rivet Nuts. When choosing, consider product quality, reputation, price, and after - sales service. Reputable fastener manufacturers usually provide high - quality products and customized solutions.